Technologies for metal surface finishing
We offer a very wide selection of technologies for surface treatment – reliable and well-proven technologies as they have been tested by many Clients in terms of quality and performance. We focus on long-term savings based on optimal exploitation. We are convinced that the price-consumption plus obtaining the most desired effect is the best equation for the success of a given technology.
Due to well-developed stock management and many years of cooperation with our suppliers, we provide deliveries within 1 working day - both to major electroplating plants and the beginning ones.
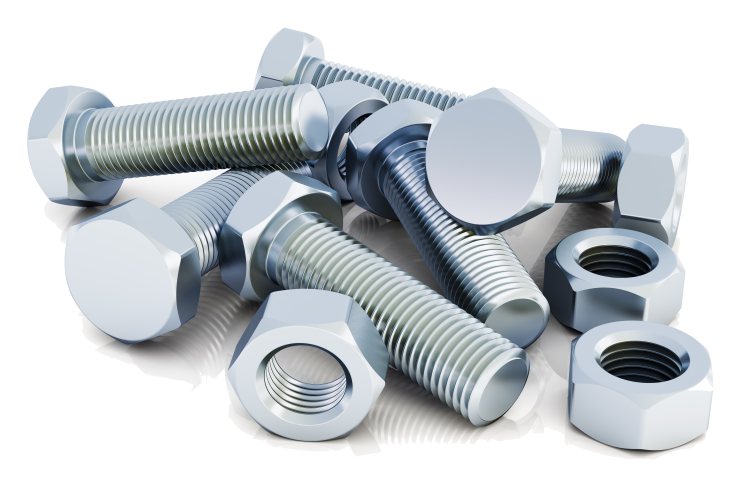
Browse our PRODUCTS
Process | Process characteristics/sub-categories |
Electrolytic cleaners | |
| |
| |
Chemical cleaners | |
| |
| |
| |
| |
Cleaner for use with ultrasonics | |
Compound increasing the efficiency of any cleaning bath |
Process | Process characteristics/sub-categories |
Acid inhibitor for pickling bath |
Process | Process characteristics/sub-categories |
Acid process | |
| |
| |
Non-cyanide alkaline Sodium-based process | |
| |
Non-cyanide alkaline Potassium-based process | |
Non-cyanide alkaline Zn-Ni process | |
|
Process | Process characteristics/sub-categories |
Free from Cr VI black passivation for Zn | |
| |
Free from Cr VI black passivation for Zn-Ni | |
Free from Cr VI blue passivation for Zn | |
| |
| |
| |
| |
| |
| |
Free from Cr VI blue passivation for Zn-Ni | |
| |
| |
Free from Cr VI yellow passivation for Zn | |
| |
| |
| |
| |
| |
Cr VI yellow passivation for Zn | |
Free from Cr VI yellow passivation for Zn-Ni |
Process | Process characteristics/sub-categories |
Bright / Mirror-bright Nickel process | |
| |
| |
| |
Semi-bright nickel layer for duplex system | |
| |
Intermediate layer for triplex system | |
Microporous layer under overlying Chromium | |
Satin Nickel process |
Process | Process characteristics/sub-categories |
Barrier Nickel layer on the Aluminium surface prior to electroless Nickel plating | |
| |
Bright phosphorus electroless Nickel process | |
| |
Semi-bright phosphorous electroless Nickel process | |
|
Process | Process characteristics/sub-categories |
Free from CR VI Chrome process | |
| |
| |
Cr VI Chrome process | |
| |
|
Process | Process characteristics/sub-categories |
Alkaline process, containing cyanide | |
| |
Acid process | |
| |
|
Process | Process characteristics/sub-categories |
White Bronze process | |
Yellow Bronze process | |
White cobalt tin | |
Cobalt tin in anthracite | |
Electrolytic brass |
Process | Process characteristics/sub-categories |
Iron | |
| |
Manganese |
Process | Process characteristics/sub-categories |
Hard platiunum process |
Process | Process characteristics/sub-categories |
Bright Silver process | |
Mirror-bright Silver process |
Process | Process characteristics/sub-categories |
Process | Process characteristics/sub-categories |
Sealer after passivation | |
| |
| |
| |
Organic sealer for Zinc | |
Organo-mineral sealer for Zinc | |
Sealer for hot Zinc process | |
Sealer after blackening of Steel | |
Organic transparent laquer applied by dip methood preventing Brass from oxidation without changing colour of originally applied coating | |
| |
Protective film | |
|
Process | Process characteristics/sub-categories |
Blackening process for Nickel, bronzing process for Brass and Copper | |
| |
Blackening process for Iron, Steel and cast-iron | |
| |
Blackening process for Stainless steel | |
|
Process | Process characteristics/sub-categories |
Degreasing and/or etching | |
| |
| |
| |
Electrocolouring | |
Dyeing | |
| |
| |
| |
Protective sealants | |
| |
| |
|
Process | Process characteristics/sub-categories |
Electrolytic anodic stripper for rack | |
|
Black is beautiful – Try our technologies!
BLACK PASSIVATION
A free from hexavalent chromium, environment-friendly, based on two components and easy-to-use process. Produces intensive black coatings on zinc deposits obtained from cyanide and chloride zinc electrolytes and is suitable both for rack and barrel applications.
Optionally, the use of dedicated topcoat/sealer will increase corrosion resistance even more, emphasize intensity of black colour and conceal scratches after barrel applications.
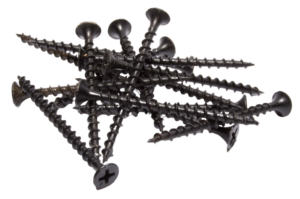
ANTHRACITE TIN-COBALT PROCESS
A unique process of applying a black anthracite coating. Suitable for bright nickel and bright copper. The process solution is highly stable and gives excellent uniform deposit and colour over wide current density range, therefore it is suitable both for rack and barrel application.
Advantages:
- high bath stability and uniform colour in wide current density range
- high corrosion resistance
- easy control of bath parameters
- excellent abrasion resistance
- easy waste-water treatment
The process is used for galvanic decorative coating of small items: jewelry, equipment, sanitary fittings, camera, watches and pens components.
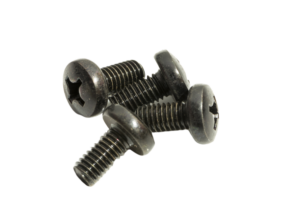
Our bestsellers
A non-cyanide alkaline zinc process distinguished for giving highly ductile deposits, without flaking and blistering even if larger thickness of deposit is involved. Suitable both for rack and barrel applications without the need to drastically adjust the basic composition. An optional additive dedicated for special cases enables obtaining deposits of thickness greater than 15-20 microns while maintaining their ductility.
This technology guarantees low operating costs while maintaining exceptional brightness. It enables operation at high electrolyte temperatures (up to 35ºC) - current density can be increased, excellent throwing power achieved and costs of electrolyte cooling reduced.
Advantages:
- greater production efficiency and reduced electrolyte costs - shorter application time and decreased total thickness of the zinc deposit necessary to cover hard-to-reach places
- flaking eliminated even when plated components are having thicker deposits
- plating of complex shapes at both high and low current density
- excellent ductility and uniform distribution in a wide range of current density
- free of binding and chelating agents
- easy waste-water treatment
The process is widely recognized in the global galvanic market, primarily due to the esthetic effect, durability of the coatings obtained and reduced bath operation costs.
This process is dedicated for use at high-temperatures (up to 45°C) installations. Produces bright ductile deposits over wide current density range and can be used for both rack and barrel applications.
Advantages::
- this technology produces a unique, stable solution with unsurpassed solubility that eliminates problems with oiling-out even at high temperatures
- produces ideal zinc deposit easy to undergo chromating process, as a result the chromate coating is uniform in terms of both thickness and colour – excellent passivation adhesion
- readily plates over malleable iron, castings, heat-treated steels
- plating of complex shapes at both high and low current density and both in rack and barrel installations
- the process ensures excellent brightness at low current density and hence proves to be an ideal process for barrel plating
A passivation process that produces light blue chromate coatings. It does not contain chromium VI, and yet it produces coatings with two to three times better corrosion resistance compared to classic hexavalent chromating process. The thickness of the chromate coating depends on the concentration of the passivation concentrate in the working solution. It can be used for passivation of zinc coatings obtained from alkaline and low acidic electrolytes, in both rack and barrel installations.
Advantages:
- the produced chromate coating is highly temperature resistant and withstands 48 hours at 120°C without influence on colour and corrosion resistance
- passivated parts withstand 80-100 hours in a salt chamber with white corrosion of not more than 5% of the reference surface
- at concentration of 155 ml \l, conversion coatings with thickness over 300 nanometers and excellent corrosion resistance are obtained
- the process is less aggressive to zinc deposits as compared to passivation based on chromium VI, which extends the longevity of working solutions
Unique organic protective coating
Our offer includes a unique laquer for rack applications that protects brass against oxidation without changing the originally applied color.
Aluminium anodizing and colouring process
Technologies that enable obtaining hard, waterproof and UV resistant coatings (not only decorative), while choosing from a wide selection of colors.